Batenburg Techniek supplies customised simulators and gets the most out of the investment.
We achieve this by using existing and already realised engineering data such as 3D drawings (mechanical) and models (MatLab, Orcaflex, Python). Or by upgrading the simulator for training purposes.
For a simulation, we often integrate separate components, such as PLC hardware, computers on which the models run, and visualisation software with VR goggles and a screen visualisation. The components together form a single simulator.
Simulations
Batenburg has extensive expertise in simulation solutions, both in mechanical engineering and process control.
We use simulations to work even more efficiently, increase the quality of the software and reduce risks in complex processes.
For the design, validation and testing of machines and systems, Batenburg Techniek frequently uses simulations. Working with simulations is also a regular feature for purposes of training and communication.
Some simulation methods are simple, such as input/output (I/O) simulations. Others, on the other hand, are very complex. If this is the case, we use physical models to ensure maximum accuracy. Using a HoloLens application, we can simulate and test, without the physical machine being present. This saves a lot of time and reduces the chance of errors. It also allows us to make a virtual copy of the real, physical machine and link it to the real controller. In industry 4.0, this is called a ‘digital twin’. Such a twin allows you to first test changes virtually before implementing them on the machine. This way, the machine can be put into operation with software that has already been tested. A major advantage!
Would you like more information?
Alex van Dalen
Managing Director
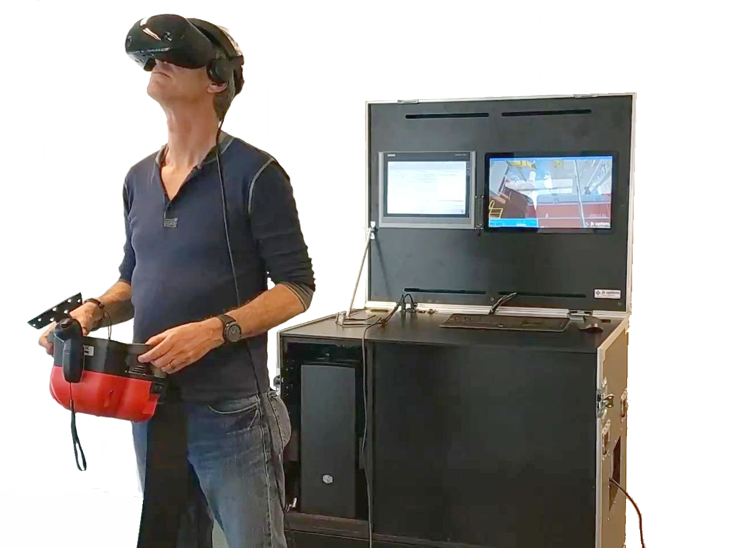
Worth the investment
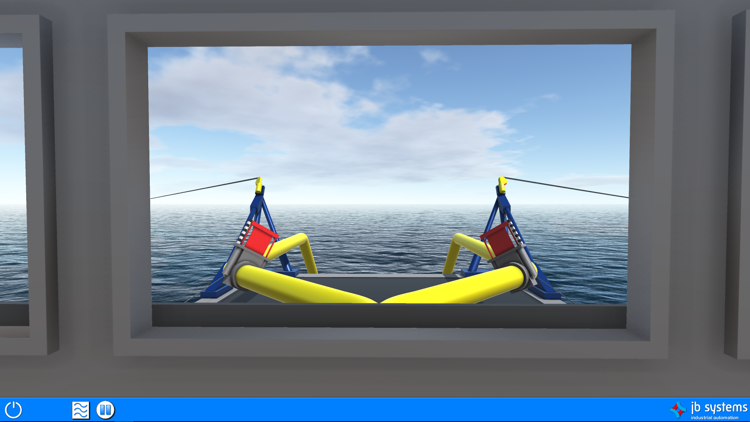
Pre-tested and quickly put into operation
A process simulator makes it easier for software engineers to test larger process components. The simulators of Batenburg Techniek actually intervene in the I/O. As a result, no modifications to the control software are required and the simulator can simply be connected to the business processes.
We also use the simulator for internals tests and the FAT. This means that new software can be commissioned significantly faster. Using the simulator as an operator training system allows a factory to practice the processes in advance with the new controller and HMI. This significantly reduces the likelihood of errors. For operators, this is the perfect preparation for the new control system!
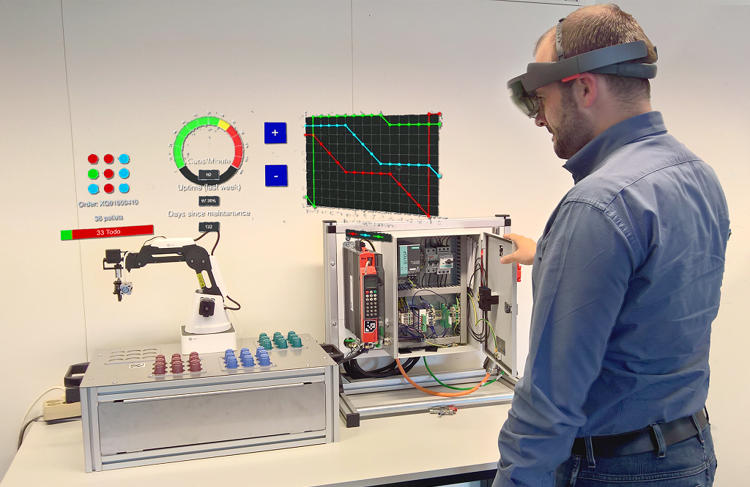
Life cycle simulation
By virtually mimicking the behaviour of a process in a plant, a process simulator can be used to simulate the entire plant process. In other words, the software will be fully tested even before being actually taken into use.